PMMA - Acrylic
PMMA – Akryl – polymethylmethacrylat – Acryl – (Trade name Plexiglas)
Information om PMMA – Acrylic thermoplastic
Application: PMMA er et amorft materiale, as more widely used, which was previously used glass. In industry mainly used the clear and smoked sheet, while the opal white and the many different colored plates especially applies in design- and advertising industry. PMMA is often used for shielding, cabinets and removable windows and other places, where the weight reasons can advantageously replace glass with acrylic. for illuminated signs, displays and decoration PMMA is a widely used material. The possibilities are almost endless, both in terms of colors and shapes. Glazing, mirrors, airplane windows, dashboard, aquariums, optical instruments, lenses, laboratoriedele, kitchen parts and light parts.
Co-extruded sheet of ABS with a top layer of acrylic ( PMMA ) Eller PMMA / ABS / PMMA, called sanitary acrylic, and used for thermoforming of bathtubs and the like.
Bending: PMMA is suitable for bending on Heat bending machines. Acrylic sheets set in the bow called cold bending. Guideline for arc minimum radius can be calculated by multiplying the plate thickness with 200. In 3 mm acrylic plate may be set up in the arc with a minimum radius of 3 mm * 200 = 600 mm.
Acrylic sheets can of course also hot bends by heating with heat gun el. or similar. The acrylic sheet is heated, until it softens, and then be bent over an edge, a tube or otherwise, that has the desired shape. The plate is held in this position, until it has cooled.
Features: Softens at temperatures above about. 100°C. PMMA is relatively rigid and strong. PMMA allows very high light transmission. Relatively good chemical resistance.
Colors: In addition to clear and smoky , manufactured acrylic also in a myriad of colors.
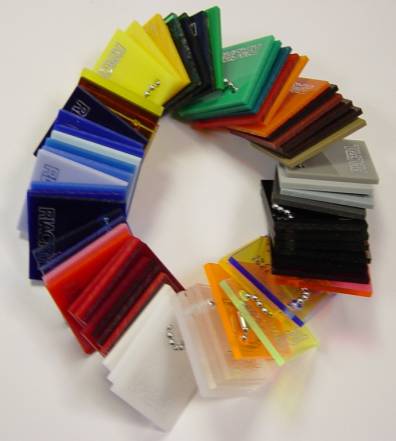
Advantages PMMA is UV-resistant and has good light transmission and is therefore suitable for outdoor applications.. In the temperature range -40 ° to + 80 ° C influenced acrylic sheets not of changing weather conditions.
The material has high rigidity and a nice surface gloss. The impact strength is 5-8 times as strong as the glass. Comparing clear acrylic glass of the same thickness, is higher for the light transmission than acrylic glass. A low weight makes glass easy to handle and work with.
Physiological properties: Can be used in contact with food. Rules can be found at FDA and BGA. Molded blocks can contain monomer.
History: I 1901 wrote Otto Röhm (picture) doctoral thesis on acrylic polymers. Otto Röhm was born in 1876 i Öhringen/Württemberg; death 1939 i Berlin. Otto Röhm founded the company Röhm & Haas A.G – Esslingen, with his friend and merchant Otto Haas. Rohm and Haas produced in 1927 PMMA to the paint industri. Molding compounds was initiated in 1933.
Identification fire test. cast PMMA: Burns with a yellow, tow other and ready crackling flame. Smells aromatic, sweet-like fruit, acrylic monomer. Acrylic is not self-extinguishing. Cast PMMA blistering but does not drip.
Identification fire test. extruded PMMA: Burns with a yellow, tow other and bright flame. Smells aromatic, sweet-like fruit, acrylic monomer. Acrylic is not self-extinguishing. Extruded PMMA blistering and drips.
Trade names: Altuglas®, Perspex®, Plexiglass®, Riacryl®
Category: amorphous material, good optical properties.
Chemical structure: as polyethylene, but with an "acrylic group" instead of one of the hydrogen atoms.
Laserskæring : Acrylic is all very well to laser cutting, providing transparent cut that do not necessarily require reworking.
Delivery: PMMA sheet is best known in the extruded version, then they have the finest tolerance. Cast slabs have the advantage, they may be prepared in thicker versions as well as in blocks. PMMA is also produced in pipes and rods, and there are several grades with special properties. Available with scratch-resistant coating.
Bonding: Acrylic can be glued with xylene – it can be purchased at paint dealers.
The acrylic can be bonded with acrylic dissolved in chloroform (no UV light).
Methylene Chloride solgt som “Plaskolite” (no UV light). Silicone can be used in conjunction with other materials, but does not have good binding to the same acrylic. by bonding, which are exposed to greater mechanical stress and exposed to UV radiation, should be used polymerisationslim.
The strength and durability of a collection depends on proper pretreatment of the surfaces, to be bonded, However, the product can often make do with minimal pretreatment. Such as. degreasing. Ideally joint surfaces should be degreased with eg. acetone, MEK or other proprietary degreasing agents, to remove all traces of the release agent, fat, dust and loose particles.
alcohol, petrol (petroleum) or paint thinners should never be used.
The strongest and most durable joints are obtained abrading or chemically etched. If sanded be degreased surfaces.
Pretreatment of PMMA should be degreased with either isopropanol or petroleum ether (b.p. 40-60 °C). Use of strong solvents such as acetone, may damage the surface of the material. Light sanding may improve adhesion .
Polishing: Flame polishing may be used as edge polishing of acrylic sheets. Cast acrylic is difficult to flame polish than extruded acrylic. It is usually less expensive to flame polish than hand polishing the edges and meet in most cases the requirements.
Diamond edge polishing used exclusively for acrylic. the goal is, to make acrylic sheet glass clear on the edge after the cut. Some machines can be adjusted in degrees.
Optical properties: Acrylic sheets have good optical properties and a light transmission of 92% for plates 3 mm thickness. By milling or engraving of the surface and polishing the edges can be obtained a very good play of light in the material.
Surface treatment: Printing by screen printing is widely used and provides good results. Colors and paint based on acrylic resins can be used. Take care when using thinner, as it can attack the material. Thorough cleaning before surface treatment is needed to ensure good adhesion. Wash with soapy water and soft, clean rags recommended.
Cleaning: When cleaning with solvents, there may be cracks usually in material. For cleaning should be used acrylic cleaner or a mild Painted surfaces should, which relaxes and prevents static electricity.
Assembly (mechanical): Avoid countersunk screws. When joining with other materials, please note that acrylic has large coefficient of expansion. (Approx.. 6 times steel.)
Cutting: Use sharp tools and clean water as coolant. Avoid sharp transitions, due kærvfølsomhed.
Welding: Varmespejl strength ca. 80%, can also be welded to the ABS, PC og SAN –
Ultrasonic welding – Hot gas welding . Welding with PMMA thread 165-185 °C. Welding with PVC wire 165-200 °C. – Friction welding – Viberation welding.
drawbacks: The surface is not as hard as glass, and will therefore be more susceptible to scratches. PMMA is a highly notch sensitive material,, which should be taken into account in connection with mechanical processing sensitive to stress cracking, alcohols e.g.. Dissolves in polar solvents.
Thermoforming :
Thermoforming of PMMA is a widely used processing method. Can be thermoformed and blow items in PMMA. The plastic is a typical amorphous material. It is very easy to thermoform. The molded outer quality, however, somewhat higher resistance than that of the extruded. The temperature for the forming of cast PMMA is between 150-180 ° C and extruded PMMA of between 140-150 ° C.
Density: 1,18 – 1,20

